Photo: Quality control at a Flex manufacturing facility for Nextracker’s patented self-powered controller.
For solar to become the dominant form of power generation and an essential part of the climate solution matrix, the focus on the intertwined value propositions of quality and reliability needs to be more than a self-congratulatory promise. The number of components and products manufactured, shipped and deployed to achieve our gigawatt and ultimately terawatt aspirations will be mind-boggling—a potential risk management headache unless the proactive and predictive quality and reliability practices are in place. It will not be acceptable to build parts and then check them for compliance, after the fact, when the cost of making that part has already been incurred. The costs of making and shipping bad parts, both monetarily and performance-wise, will be too high. Failure is not an option when our livelihood—and our planet—is at risk.
The good news is, many tests and tools, both in the factory and in the field, are already available to ensure that the dream of the clean energy transition doesn’t become a quality and reliability nightmare. At Nextracker, we’re already putting these best practices in place—something we encourage all serious stakeholders to implement as well.
One of the keys to ensuring fewer defects and variations across an exponentially increasing number of parts and components is extending aggressive statistical process control and quality management systems from the upper reaches of the supply chain down to the field. Nextracker has been taking a more proactive approach, moving upstream into the actual manufacturing processes of our partners so that we have an indication prior to the completion of the production process whether or not it meets our requirements.
The implementation of our Quality Control Assessment Tool (QCAT) has been well-received by our major suppliers. We are getting data, we are generating reports, and we are driving action items for improvement based on QCAT (see below chart). The long-term vision is to be able to reliably and consistently verify that the produced part meets all of our needs prior to shipping. We also have a much better sense of which suppliers are meeting our quality control needs right now (which is the vast majority of them) and which ones need to improve.
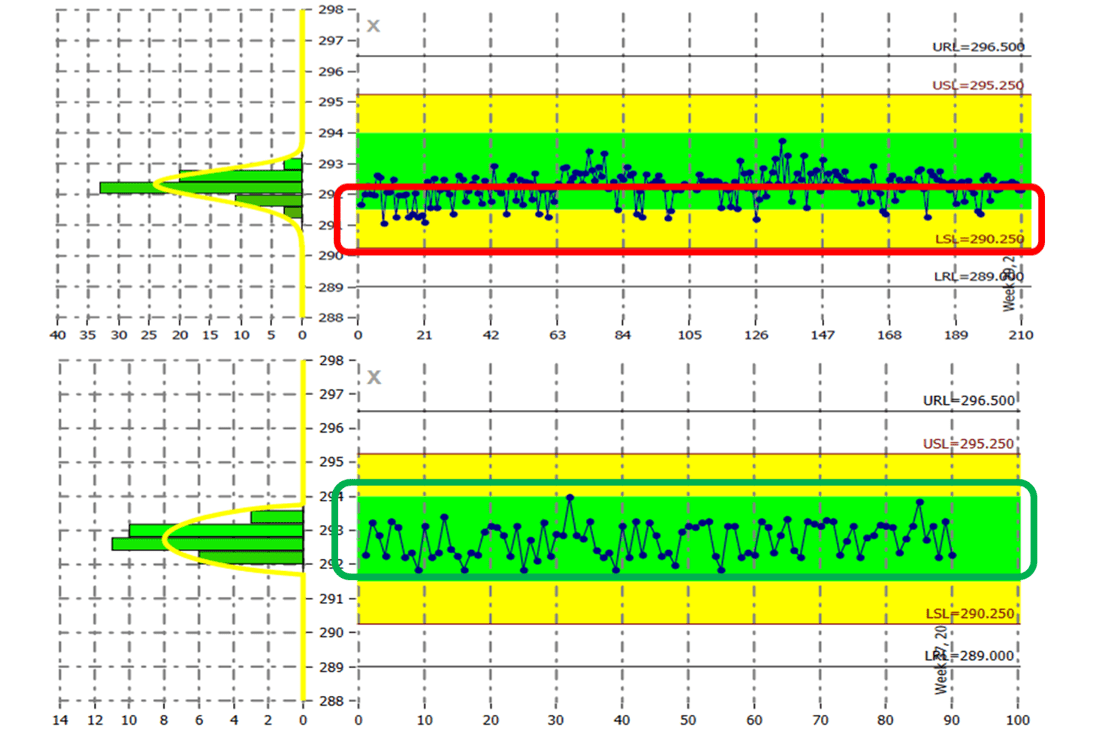
As this example shows, the quality control assessment monitoring tool has helped identify the risk of a lower specification limit excursion to help recenter the process.
Our supply partners really want to do the right thing because they know the financial success of their company depends on it. It’s a win-win—if they’re successful, we’re successful, and vice versa. They’re also seeing the value of us having a second set of eyes on their production process to help them avoid the costs associated with making defective or substandard parts. That’s a positive relationship, which will ultimately lead to confirmation that critical-to-quality elements are being met in production so that only good parts reach the end of the process.
Ongoing standards and testing work are also raising the bar for meeting the quality and reliability challenges for the gigawatt age. For example, I’ve been working with an Underwriters Laboratory (UL) task group on improving corrosion testing of solar tracker parts. We’re in the process of doing side-by-side testing of various material coatings, fasteners, and the like, and using two different testing scenarios to look at whether or not the outcomes are supported by what we see in the field. Thus far, we’ve identified a disconnect between the way that people have been doing corrosion testing and the real-world conditions experienced by trackers in the field. This kind of work will help ensure that our products stand up to the rigors of performing as they should for the 30-year-plus lifetimes of utility-scale solar power plants.
Quality and reliability will be recurring themes in Nextracker outreach and content this year. Future posts in this blog series will take a deeper dive into our QCAT program as well as explore the intersection of quality, reliability, logistics and sustainability. In the coming weeks, the second installment of our “Mitigating Extreme Weather Risk” white paper series will be published, examining how differentiated utility-scale solar project and tracker design and control strategies can protect against high wind events and dynamic wind effects.
We’ll be participating in the virtual NREL PV Reliability Workshop later this month, where I’ll be talking about reevaluating hail impact testing for PV modules and other topics. I’m also a co-author of a new paper in the IEEE journal Progress in Photovoltaics, which examines work on improving the standards for assessing PV modules durability and performance in high-temperature environments on different types of mounting structures. In case there wasn’t enough going on, Nextracker is also pushing down the path to ISO 9001 accreditation for our quality management system.
When it comes to maintaining a high level of quality and reliability practices and continuously improving them, every Nextracker team member is all in. We know what’s at stake.
Kent Whitfield has been involved in a range of PV activities from testing, analysis and certification through product manufacturing, system design and deployment for 30 years. He is a VP for Quality at Nextracker where he oversees global quality and durability. He has previously been a R&D manager and principal engineer and for renewable energy technologies at Underwriters Laboratories and held Sr. Director roles in Engineering, Reliability, and Quality for Beamreach, SunEdison, Solaria and MiaSole. He has created two ISO/IEC accredited testing and certification laboratories and represents the USA for IEC standard development for PV products.